Slip-on flange: sealing principle & what should be noticed (part 2)
Forging of slip-on flanges can be categorized into rotary forging, roll forging, cross-wedge rolling, rotary swaging, etc. based on the movement mode. For improving the utilization rate of materials, roll forging and cross-wedge rolling can be used as pre-processing methods for long and thin materials. Just like open-die forging, rotary swaging is also partially formed, which has little demand for force and it is possible to finish complex forgings with one or a few processes. Since there is no burr, the stressed area of forgings and the required load are both reduced. When slip-on flanges are processed by this type of forging, or open-die forging, the materials will expand from the vicinity of the mold surface to the free surface. Therefore, it is difficult to ensure accuracy. For this problem, using computers to control the moving direction of the forging die and swaging can help you obtain the final products with a complex shape and high precision.
Slip on flange forging can also be divided into open die forging, closed die forging, upsetting, extrusion, closed die upsetting. In general, forging in a temperature region where recrystallization is performed is called hot forging, and forging at room temperature without heating is called cold forging. When the slip-on flange is forged at low temperature, the dimensional change of the forging is small. At 700 °C or less, the formation of scale is small, and there is no decarburization on the surface.
The main function of slip-on flanges:
1. They are easy to detach and detect when there is a failure in the pipeline;
2. Connect the pipeline and maintain a good sealing performance;
3. If there is a problem with a certain pipeline, it is convenient to replace it.
Slip on flanges have certain technical requirements and parameters in production and use, and are processed according to certain methods. The butt weld of the ring should be post weld heat treated and inspected by 100% ray or ultrasound that meet the Class II requirement of JB4730, Class I requirements of JB4730, respectively. The welding flange should be produced under certain welding standards and techniques, in line with the corresponding national production standards and requirements; The steel plate for producing slip-on flange should follow the quality requirements and be ultrasonically inspected to ensure that there is no delamination defects, poor quality, and performance problem; The steel plate should be cut into strips along the rolling direction of the steel, bent and butt welded into a ring shape, and the surface of the steel material forms a cylindrical surface. In the production of slip-on flanges, steel plates should not be directly machined into neck flanges.
Compared with other flanges, slip-on flanges have smaller size and lighter weight, and more importantly, the joints of slip-on flanges have good sealing performance. In addition, the flange gasket has been replaced by a sealing ring to ensure that the sealing surfaces can be matched. In this way, only a small amount of pressure is required for pressing the cover tightly. As the required pressure is reduced, the size and required number of bolts can be reduced accordingly. Therefore, the slip-on flange is a relatively high-quality product which reduces the weight, space, and plays an important role in industrial use. However, the main design disadvantage of slip-on flanges is that they are not guaranteed to be leak-free because the connection is dynamic, and cyclic loads such as thermal expansion and undulations cause movement between the flange faces, affecting the function of the flange, thereby impairing the integrity of the flange and ultimately leading to leakage. So companies should try to improve the performance of products.
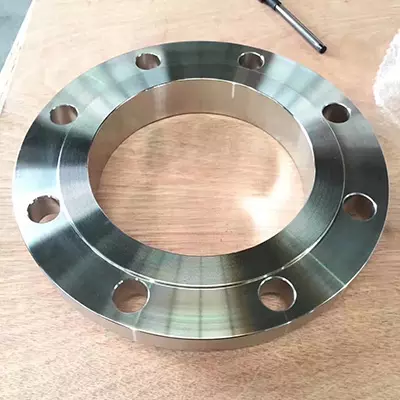
Slip on flange forging can also be divided into open die forging, closed die forging, upsetting, extrusion, closed die upsetting. In general, forging in a temperature region where recrystallization is performed is called hot forging, and forging at room temperature without heating is called cold forging. When the slip-on flange is forged at low temperature, the dimensional change of the forging is small. At 700 °C or less, the formation of scale is small, and there is no decarburization on the surface.
The main function of slip-on flanges:
1. They are easy to detach and detect when there is a failure in the pipeline;
2. Connect the pipeline and maintain a good sealing performance;
3. If there is a problem with a certain pipeline, it is convenient to replace it.
Slip on flanges have certain technical requirements and parameters in production and use, and are processed according to certain methods. The butt weld of the ring should be post weld heat treated and inspected by 100% ray or ultrasound that meet the Class II requirement of JB4730, Class I requirements of JB4730, respectively. The welding flange should be produced under certain welding standards and techniques, in line with the corresponding national production standards and requirements; The steel plate for producing slip-on flange should follow the quality requirements and be ultrasonically inspected to ensure that there is no delamination defects, poor quality, and performance problem; The steel plate should be cut into strips along the rolling direction of the steel, bent and butt welded into a ring shape, and the surface of the steel material forms a cylindrical surface. In the production of slip-on flanges, steel plates should not be directly machined into neck flanges.
Compared with other flanges, slip-on flanges have smaller size and lighter weight, and more importantly, the joints of slip-on flanges have good sealing performance. In addition, the flange gasket has been replaced by a sealing ring to ensure that the sealing surfaces can be matched. In this way, only a small amount of pressure is required for pressing the cover tightly. As the required pressure is reduced, the size and required number of bolts can be reduced accordingly. Therefore, the slip-on flange is a relatively high-quality product which reduces the weight, space, and plays an important role in industrial use. However, the main design disadvantage of slip-on flanges is that they are not guaranteed to be leak-free because the connection is dynamic, and cyclic loads such as thermal expansion and undulations cause movement between the flange faces, affecting the function of the flange, thereby impairing the integrity of the flange and ultimately leading to leakage. So companies should try to improve the performance of products.
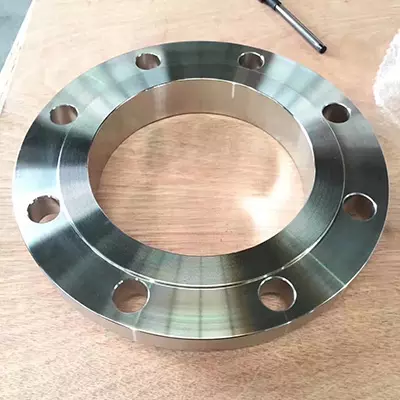