Slip-on flange: sealing principle & what should be noticed (part 1)
Sealing principle
The two sealing faces of the screw press against the flange gasket and form a seal, but this also causes damage to the seal. So, in order to maintain the seal, the screw bolts, as well as nuts that match them should be bigger for a larger screw force. Bolts with a larger diameter are needed to create the conditions for tightening the nuts, however, the larger the diameter of the bolt is, the more easily the flange will bend. The only way is to increase the wall thickness of the flange. But the entire device will have great size and weight, which becomes a special problem in the offshore environment, where weight is always a major concern. Moreover, the seal of a slip-on flange is fundamentally ineffective, which requires 50% of the bolt load to be used to squeeze the gasket, so the load used to maintain the pressure is only 50%.
Slip-on flanges are often used in situations where the medium temperature and pressure are not high and the medium is corrosive. According to the structure, they can also be threaded or welded. Flange joints consist of a pair of flanges, a gasket and a number of bolts and nuts.
What should be noticed
The steel plates for producing slip-on flanges should be ultrasonically detected to ensure that they are with no lamination defects, but good quality and performance. In order to avoid quality problem in production and use, the production and inspection of the steel plates should follow certain quality requirements. The steel plates should be cut into strips along the rolling direction, welded into a ring shape and forms a cylindrical surface. When producing slip-on flanges, steel plates should not be directly machined into neck flanges, and they should be manufactured by certain processes.
When the slip-on flange is welded by the one-side continuous welding method, the circumferentially heated part of the flange welding area will greatly compress due to the cooling of the weld seam, which further aggravates the expansion of the deformation, and the flange forms an irregular ellipse (partially concave and partially convex) in the circumferential direction. At the same time, due to the welding contraction force, the inner circumference of the flange becomes smaller, while the outer side of the flange is at a lower temperature, the welding heat has little influence, so the rigidity is better, and there is basically no contraction. This causes the cross-section of the flange twisting. And the central axis of the flange bolt hole is no longer parallel to the cylinder axis. It turns out that the force of this is very large, and after the welding of the flange section bevel and the barrel body, it is still impossible to make any change in this deformation.
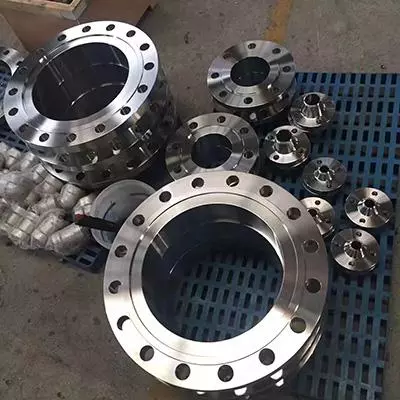
The two sealing faces of the screw press against the flange gasket and form a seal, but this also causes damage to the seal. So, in order to maintain the seal, the screw bolts, as well as nuts that match them should be bigger for a larger screw force. Bolts with a larger diameter are needed to create the conditions for tightening the nuts, however, the larger the diameter of the bolt is, the more easily the flange will bend. The only way is to increase the wall thickness of the flange. But the entire device will have great size and weight, which becomes a special problem in the offshore environment, where weight is always a major concern. Moreover, the seal of a slip-on flange is fundamentally ineffective, which requires 50% of the bolt load to be used to squeeze the gasket, so the load used to maintain the pressure is only 50%.
Slip-on flanges are often used in situations where the medium temperature and pressure are not high and the medium is corrosive. According to the structure, they can also be threaded or welded. Flange joints consist of a pair of flanges, a gasket and a number of bolts and nuts.
What should be noticed
The steel plates for producing slip-on flanges should be ultrasonically detected to ensure that they are with no lamination defects, but good quality and performance. In order to avoid quality problem in production and use, the production and inspection of the steel plates should follow certain quality requirements. The steel plates should be cut into strips along the rolling direction, welded into a ring shape and forms a cylindrical surface. When producing slip-on flanges, steel plates should not be directly machined into neck flanges, and they should be manufactured by certain processes.
When the slip-on flange is welded by the one-side continuous welding method, the circumferentially heated part of the flange welding area will greatly compress due to the cooling of the weld seam, which further aggravates the expansion of the deformation, and the flange forms an irregular ellipse (partially concave and partially convex) in the circumferential direction. At the same time, due to the welding contraction force, the inner circumference of the flange becomes smaller, while the outer side of the flange is at a lower temperature, the welding heat has little influence, so the rigidity is better, and there is basically no contraction. This causes the cross-section of the flange twisting. And the central axis of the flange bolt hole is no longer parallel to the cylinder axis. It turns out that the force of this is very large, and after the welding of the flange section bevel and the barrel body, it is still impossible to make any change in this deformation.
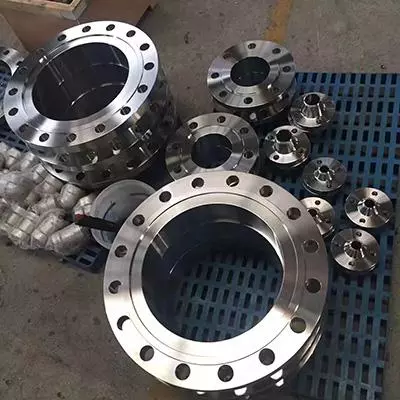