An Introduction of Common Steel Pipe Manufacture Methods
Steel pipes can be categorized into welded and seamless types. The following introduces several common steel pipe production methods.
Seamless pipe
Seamless pipe is produced without a seam or weld in the circumference. Seamless pipe is produced by a variety of methods. To put it in its most simple terms, seamless pipe is produced by piercing a solid billet of deoxidized and conditioned steel, which has been properly prepared and heated to the proper temperature. It is then processed through a series of mills where the pipe is finished to its prescribed dimensions. Seamless pipes over 14-inch are usually rotary rolled from 14-inch seamless shells which expand the diameter and reduce the wall thickness to the approximate dimensions required. Small sizes of seamless pipe are generally obtained through the use of a stretch reduced mill. In this process, the outside diameter and the wall thickness of the pipe is reduced through a series of rolls. Seamless pipe goes through various finishing operations including straightening, inspection, testing, and end finishing. Seamless pipe is widely used in construction, oil refining, chemical and petro-chemical industries.
Continuous welded pipe
Continuous welded pipe poduction begins with coiled skelp of the required width and thickness for the size and weight of pipe to be made. Successive coils of steel are welded end to end to form an endless ribbon of steel. The coiled steel is fed into a roll leveler and then into a gas fired furnace where it is heated to the required temperature for forming and welding. The forming rolls at the exit end of the furnace shape the heated skelp into an oval. The edges of the skelp are then firmly pressed together by welding rolls to obtain a forged weld. The heat of the skelp, combined with the pressure exerted by the rolls form the weld. No metal is added in the operation. The final rolls on the mill reduce the diameter and wall thickness to bring the pipe to its finished dimensions. The pipe is then cooled, descaled, straightened, inspected, tested hydrostatically, coated as required and end finished. Continuous welded pipe is commonly used for the conveyance of water, air, gas, steam, for sprinkling systems, water wells, fencing, and a multitude of structural applications.
Double submerged arc welded pipe
Double submerged arc welded pipe (DSAW) derives its name from the welding process wherein the welding arc is submerged in flux while the welding takes place. Both inside and outside welds are required and are usually accomplished in separate processes. These separate welds consume a portion of the other resulting in a single high quality weld nugget. DSAW pipe is produced in sizes from 18 inch through 72 inch and wall thicknesses from 0.250 inch through 1.5 inch.
Two different processes are used to manufacture DSAW pipe: the pyramid rolls method, and the U-O-E method. The difference in the processes is found only in the method of forming the cylinder. In the pyramid rolls process the cylinder is formed between 3 rolls arranged in a pyramidal fashion. As the name implies, the U-O-E method uses a "U" press, and "0" press for forming. Other parts of the process such as finishing and inspection are similar. Both processes use flat steel plate as the raw material.
DSAW pipe is normally produced in double random lengths with square or beveled end for welding. It is usually furnished barely but varnish is also offered. A wide range of external coatings and internal linings are available with DSAW pipe. DSAW pipe is used in high pressure gas and oil transmission lines (both onshore and offshore), structural members and pipe piles.
Spiral welded pipe
Spiral welded pipe, as the name implies, is a steel pipe which has a seam running its entire length in a spiral form. In the past, due to the method of manufacture, spiral welded pipe was relegated to low pressure and structural applications. With the development of the submerged arc welding process, the production of large hot rolled coils of sufficient width and the development of dependable non-destructive testing methods, it is now possible to produce spiral weld pipe for high pressure service.
Because of the method of manufacture, pipes with wide variety of diameters can be produced. The diameter tolerance is small, particularly with regard to ovality, and the pipe, due to its axial symmetry, has an inherent straightness. The length range is infinite and is controlled only by the cost of transportation. Spiral welded pipe is used for slurry, water and other pipelines, as well as piling and structural applications. Spiral welded pipe is produced in accordance with the dimensional and tolerance requirements of various ASTM, AWWA, and API Specifications.
Seamless pipe
Seamless pipe is produced without a seam or weld in the circumference. Seamless pipe is produced by a variety of methods. To put it in its most simple terms, seamless pipe is produced by piercing a solid billet of deoxidized and conditioned steel, which has been properly prepared and heated to the proper temperature. It is then processed through a series of mills where the pipe is finished to its prescribed dimensions. Seamless pipes over 14-inch are usually rotary rolled from 14-inch seamless shells which expand the diameter and reduce the wall thickness to the approximate dimensions required. Small sizes of seamless pipe are generally obtained through the use of a stretch reduced mill. In this process, the outside diameter and the wall thickness of the pipe is reduced through a series of rolls. Seamless pipe goes through various finishing operations including straightening, inspection, testing, and end finishing. Seamless pipe is widely used in construction, oil refining, chemical and petro-chemical industries.
Continuous welded pipe
Continuous welded pipe poduction begins with coiled skelp of the required width and thickness for the size and weight of pipe to be made. Successive coils of steel are welded end to end to form an endless ribbon of steel. The coiled steel is fed into a roll leveler and then into a gas fired furnace where it is heated to the required temperature for forming and welding. The forming rolls at the exit end of the furnace shape the heated skelp into an oval. The edges of the skelp are then firmly pressed together by welding rolls to obtain a forged weld. The heat of the skelp, combined with the pressure exerted by the rolls form the weld. No metal is added in the operation. The final rolls on the mill reduce the diameter and wall thickness to bring the pipe to its finished dimensions. The pipe is then cooled, descaled, straightened, inspected, tested hydrostatically, coated as required and end finished. Continuous welded pipe is commonly used for the conveyance of water, air, gas, steam, for sprinkling systems, water wells, fencing, and a multitude of structural applications.
Double submerged arc welded pipe
Double submerged arc welded pipe (DSAW) derives its name from the welding process wherein the welding arc is submerged in flux while the welding takes place. Both inside and outside welds are required and are usually accomplished in separate processes. These separate welds consume a portion of the other resulting in a single high quality weld nugget. DSAW pipe is produced in sizes from 18 inch through 72 inch and wall thicknesses from 0.250 inch through 1.5 inch.
Two different processes are used to manufacture DSAW pipe: the pyramid rolls method, and the U-O-E method. The difference in the processes is found only in the method of forming the cylinder. In the pyramid rolls process the cylinder is formed between 3 rolls arranged in a pyramidal fashion. As the name implies, the U-O-E method uses a "U" press, and "0" press for forming. Other parts of the process such as finishing and inspection are similar. Both processes use flat steel plate as the raw material.
DSAW pipe is normally produced in double random lengths with square or beveled end for welding. It is usually furnished barely but varnish is also offered. A wide range of external coatings and internal linings are available with DSAW pipe. DSAW pipe is used in high pressure gas and oil transmission lines (both onshore and offshore), structural members and pipe piles.
Spiral welded pipe
Spiral welded pipe, as the name implies, is a steel pipe which has a seam running its entire length in a spiral form. In the past, due to the method of manufacture, spiral welded pipe was relegated to low pressure and structural applications. With the development of the submerged arc welding process, the production of large hot rolled coils of sufficient width and the development of dependable non-destructive testing methods, it is now possible to produce spiral weld pipe for high pressure service.
Because of the method of manufacture, pipes with wide variety of diameters can be produced. The diameter tolerance is small, particularly with regard to ovality, and the pipe, due to its axial symmetry, has an inherent straightness. The length range is infinite and is controlled only by the cost of transportation. Spiral welded pipe is used for slurry, water and other pipelines, as well as piling and structural applications. Spiral welded pipe is produced in accordance with the dimensional and tolerance requirements of various ASTM, AWWA, and API Specifications.
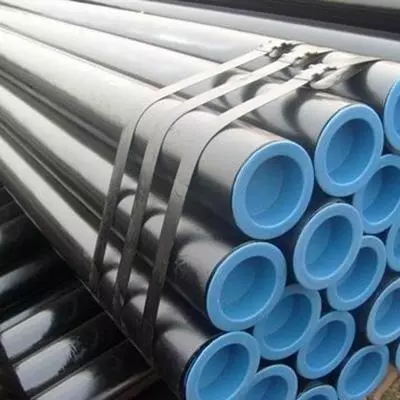